Overview
The briquette machine is mainly used for refractory, power plant, metallurgy, chemistry, energy, transportation, heating, and other industries. Its finished product is eco-friendly, and easy to transport, which improves the utilization of waste and contributes to excellent economic and social effects.
Applicable Materials
all kinds of powder, waste and residue such as pulverized coal, iron powder, coking coal, aluminum powder, iron filings, iron-based oxide scale, carbon powder, carbon powder, slag, gypsum, tailings, sludge, kaolin, activated carbon and coke. The finished product is eco-friendly, and easy to transport, which improves the utilization of waste and contributes to excellent economic and social effects.
Working Principle
After the main body is powered by an electromagnetic speed regulating motor, the material is transmitted to the drive shaft via a pulley, a cylindrical gear speed reducer and a pin coupling. The screw feeding device is driven to rotate under the force of the pulley and of the worm speed reducer and then presses the material into the main feeding port. When the amount of material fed by the screw feeder meets the requirement of the machine, the feeding pressure can be maintained constant to ensure high product quality. If the feeding amount is too large, the feeding device will be overloaded; contrarily, a small amount of material cannot form a ball. Therefore, the skilled operation is an essential factor for its normal running.
Instructions for the briquette production line
To produce high quality briquettes needs first-class coal and binders, high-quality equipment and excellent production processes. As is known, the requirement for briquette coal making is that the powder whose size is less than 0.074mm account for 50-70%, 1-2mm for 20-30% and 0-3mm for about 20%. If the powder is too large, it is easy to burst when sent into the furnace; if it is too fine, operators must add more binder, which tend to increase investment cost. Furthermore, temperature also shapes the pulverized coal’s size. Therefore, it is essential to choose a right pulverizer. As the intermediate process, stirring has another function of kneading. The molding machine is the most significant part in the production line. Hence, there are some points need to be paid attention to when choosing a right machine.
Firstly, the required pressure is influenced by coal’s size and shape as well as balls ‘size and shape. Users had better select the machine with adjustable molding pressure according to your economic conditions.
Secondly, since the roll cover plays a significant role in the overall service life, it is advised to choose a machine with the wear-resistant alloy roll.
Thirdly, finished products must be dried before being sold or used. At present, the vertical dryer, the flap and mesh belt dryer are widely accepted in the market for their high efficiency.
leave message
Advantages
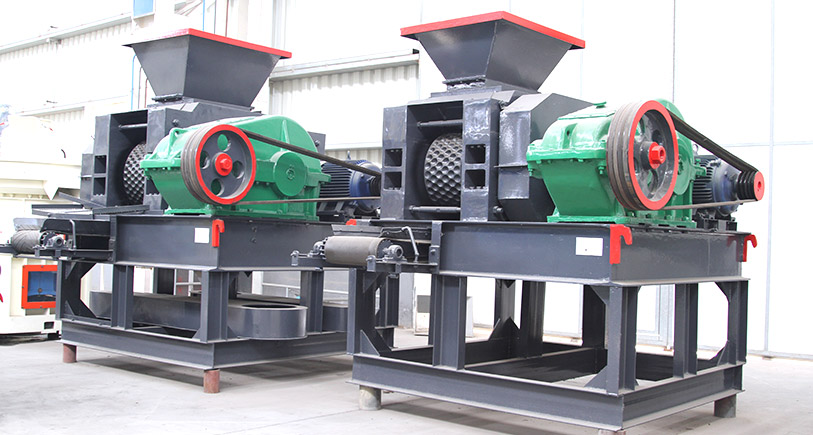
100 t/h briquette making machine
Fote briquette press machine is designed to continuously work for 24 hours without interruption. With a lubricating system, precise processing of spare parts and steel components, the machine can be operated for a long time.
The equipment is made of excellent steel materials with advanced heat treatment in the strict process, notably key components that are made of special materials, which ensures strong resistance to friction and wear as well as long service life.
Thanks to the compact structure, the press machine runs smoothly and safely without strong vibration or high noise.
The gear reducer is the center of the speed shifting drive of the briquette making machine. We independently designed and assembled all types of speed reducers branded Zhongzhou, which are made of fine steel materials in the strict process and have the fault rate of less than 1%.
In light of the large weight, the spindle in wide diameter, the bearing in large mode and high-quality steel parts, the machine inelastically but perfectly matches other equipment without any tremor and has higher pressure of 10kg/m2 than similar products.
What makes our briquette press machine different from common ones is we design it by taking possible maintaining problems into consideration to ensure less tightness of large workpieces. Otherwise, it will be more difficult for customers to dissemble and maintain if they are too firm.
The briquette maker features large weight, high pressure caused by the hydraulic system and precise manufacturing and assembly, which enhances the forming rate and the weight of finished products. Also, it has an extremely low crushing rate. It is not easy to catch fire in the drying process.
The hydraulic briquette press machine has high hydraulic pressure and adopts Fote brand hydraulic system for the system meets the national standard. In addition, the forklift is used for the cylinder and the piston is quenched. The oil pump is a state-owned product with stable performance. Therefore, the hydraulic system that was developed over ten years ago can be still in normal operation.